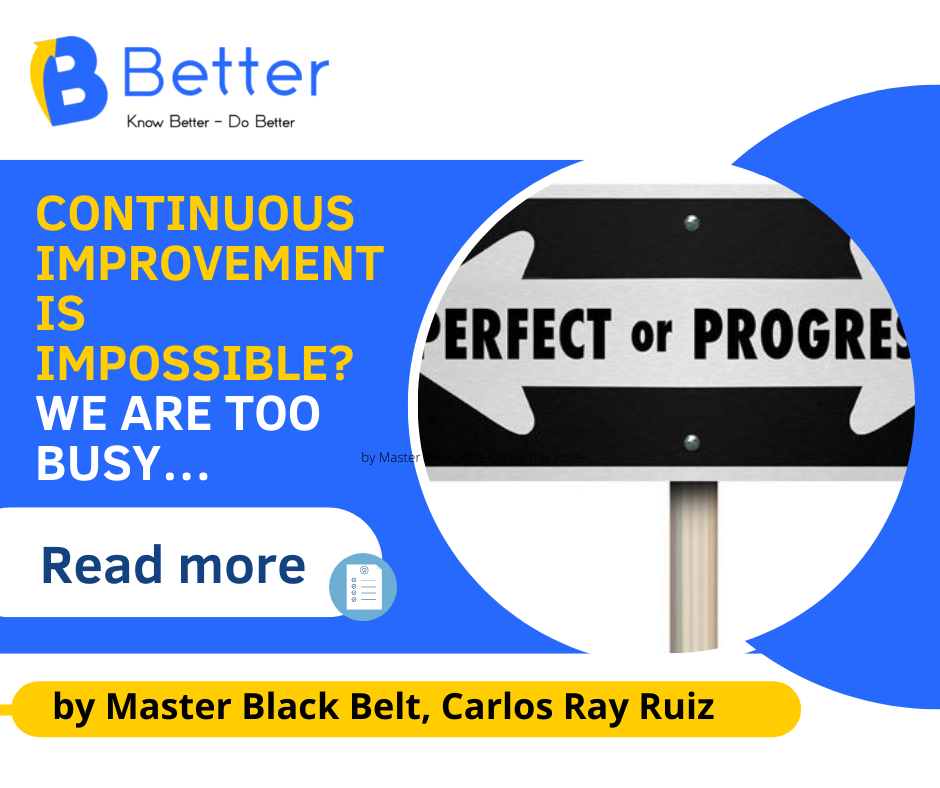
by Master Black Belt, Carlos Ray Ruiz
3 Lessons Learned on how to implement Continuous Improvement in the midst of many other “important” things I need to do.
A lot has been said and written about Continuous Improvement (C.I.). But it is always good to go back and review some of the definitions that exist out there in regard to C.I. Here is one that I like:
According to the Institute of Quality Assurance “continuous improvement is defined as a gradual never-ending change which is: ‘… focused on increasing the effectiveness and/or efficiency of an organization to fulfill its policy and objectives. It is not limited to quality initiatives. Improvement in business strategy, business results, and customer, employee, and supplier relationships can be subject to continual improvement. Put simply, it means ‘getting better all the time.’ “
As you can see the term Continuous Improvement is broad and perhaps that is one of the things I like about it. People have asked me to narrow or change my job title (Director of Continuous Improvement) or to use a different name for some of the initiatives that I am leading and to substitute the term Continuous Improvement for something else. Some have requested me to call it Process Improvement, Process Excellence, Lean Six Sigma, Lean, or Operational Excellence, the reason why I wouldn’t want to change it is the fact that I see Continuous Improvement as a holistic approach that allows people to concentrate in the “improvement process” that takes place with processes but also with us as people. Continuous Improvement presents an opportunity to identify improvement opportunities in areas like leadership, problem-solving, conflict resolution, etc. If you think about it, everything is susceptible to be improved, and to me, that is the beauty of why Continuous Improvement is a very powerful idea that every organization should embrace.
I believe that one of the authors that better captures the essence of what Continuous Improvement is about is author and professor Masaki Imai ( https://en.wikipedia.org/wiki/Masaaki_Imai ). He likes to speak about Continuous Improvement in very simple terms. I like this because it helps people and leaders to more easily understand what Continuous Improvement is all about. Let me share a quote from Masaaki Imai that reflects what I mean:
“The message of the Kaizen (C.I.) strategy is that no a day should go by without some kind of improvement being made somewhere in the company” – Masaaki Imai
I often tell people that C.I. is simple but it is difficult. Let’s take the example of the last company where I tried to implement Continuous Improvement. One of the biggest challenges that I had to face was people not doing Continuous Improvement because they were “busy”. Of course, a Continuous Improvement practitioner will ask a follow-up question….. You are busy doing what? just to discover that many people are busy doing activities that do not necessarily add value. This will lead us to explain that from a Continuous Improvement perspective a “value add activity” refers to activities that will transform raw material or information to meet true customer requirements.
So then the question becomes how do you implement a Continuous Improvement strategy or even a C.I. project in the middle of so many other competing priorities that you and your teams experience every day?
So here are 3 lessons that I have learned that perhaps will help you in your effort to implement or deploy a successful Continuous Improvement strategy.
1. Don’t use Continuous Improvement to clean windows.
This is a phrase that I heard a long time ago. It means that it is critical to make sure that your Continuous Improvement strategy and projects are aligned with your Highly Important Goals. If you are able to connect your improvement efforts with what is most important to you and your organization then it becomes harder to find excuses to dedicate time to implement your Continuous Improvement projects because you are “too busy.”
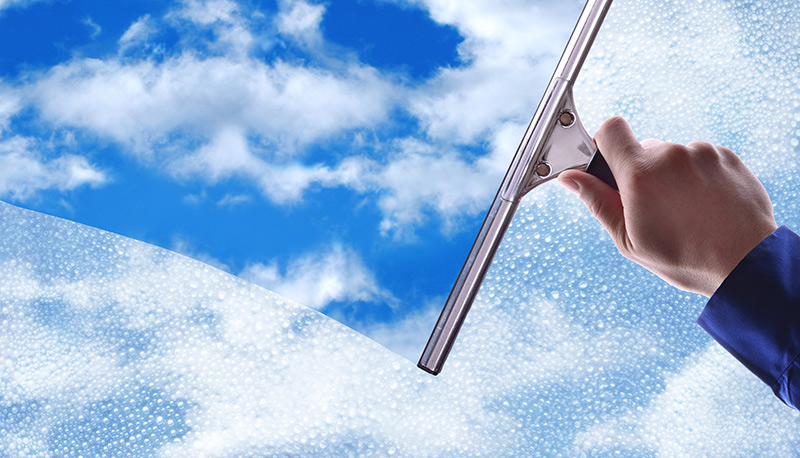
2. Discipline and Accountability.
It is easy to get excited especially when you are implementing a new initiative, a new tool, or a great principle, however, the challenge is always how to sustain the level of commitment over a long period of time. It is very important to establish a system of accountability that will allow you and your team to continually look at the progress, obstacles and lessons learned that you and your team have achieved. Tier reviews are a great way to ensure that the right level of accountability is helping you to be successful. So for example, if you have 3 hierarchy levels in your organization (Executives, managers, and team leaders), you could find ways to have each of those levels involved in the C.I. process.
Tier 1, team leaders will need to closely review and monitor the progress of the C.I. projects that are taking place within the team. Tier 2, the area manager will have to understand the overall status of the progress that each of the team leaders is demonstrating in the area of C.I., and tier 3, the general manager or director needs to understand what are some of the obstacles that the managers and the teams are facing during the implementation of their improvement in order to help them clear the path to make sure the projects are successfully implemented.
The tier meetings may look different depending on the way the company is structured however the point is that it is important to develop a system of discipline and accountability that will ensure the effectiveness and sustainability of the improvement projects. The organizations that have succeeded in their efforts to implement Continuous Improvement have made Continuous Improvement a foundation to their regular operational model, this will ensure that the C. I. efforts are front and center and it will ensure that the leaders are serving their teams by helping them remove the barriers that the staff faces when trying implement changes that challenge the status quo.
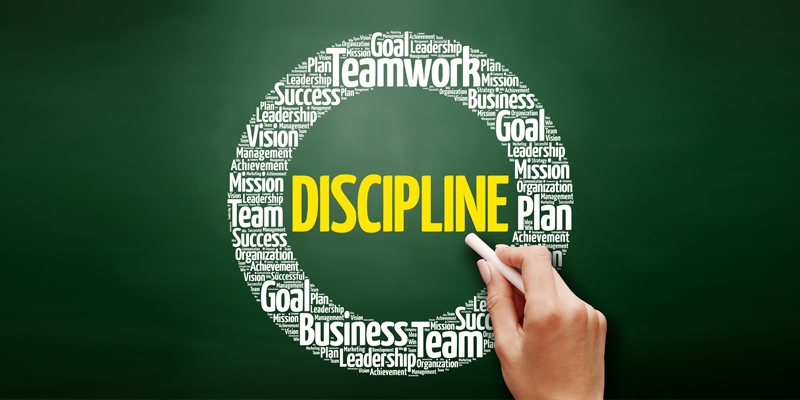
3. Don’t let perfection get in the way of better.
One of the biggest challenges that people face when trying to implement a Continuous Improvement culture has to do with how to deal with imperfection. Think about it. If you are doing Continuous Improvement you are going to constantly try new things. This will result in mistakes and failures. Therefore the scope for each of those improvement projects is very important. So instead of defining projects that could potentially last 2 years, the question is how to break down the project so that you begin to see results as soon as possible (weeks to maximum 6 months). This will help the team to gain and keep momentum and it will allow the team to experience success. Especially in manufacturing, you can tell when a company has a Continuous Improvement culture when you notice that they mark the layout using tape vs oil paint. That means that they know things will change so they need to make those changes as easy and quick as possible. Compare that in a service or transactional organization where the organization needs to develop standard operating procedures and develop a 20-page perfect manual, vs developing a one-page quick procedure or even a 5 minutes video explaining to people how to do the work.
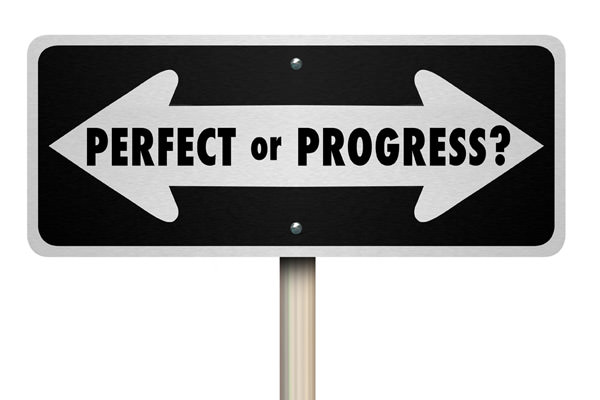
In summary…
Continuous Improvement deals with the process of how to improve anything. So the more you learn about the Continuous Improvement process, the more you will recognize its transformational power. I have seen firsthand how many organization wants to implement “fancy” innovation, agile or you name it, strategies without spending the right amount of time and resources building a Continuous Improvement culture. In my experience when an organization does this, they will have to deal with the consequences of choosing the “silver bullet”, versus the effort and dedication that involves developing a Continuous Improvement culture. The execution and the sustainability of those innovative, agile, or you name it, projects become extremely hard since the staff and the leaders have not developed the muscle to deal with change. Continuous Improvement is a simple yet difficult way to approach business because it will require humbleness on the side of the staff and the leaders to continually take risks, make/embrace mistakes and learn from those mistakes.