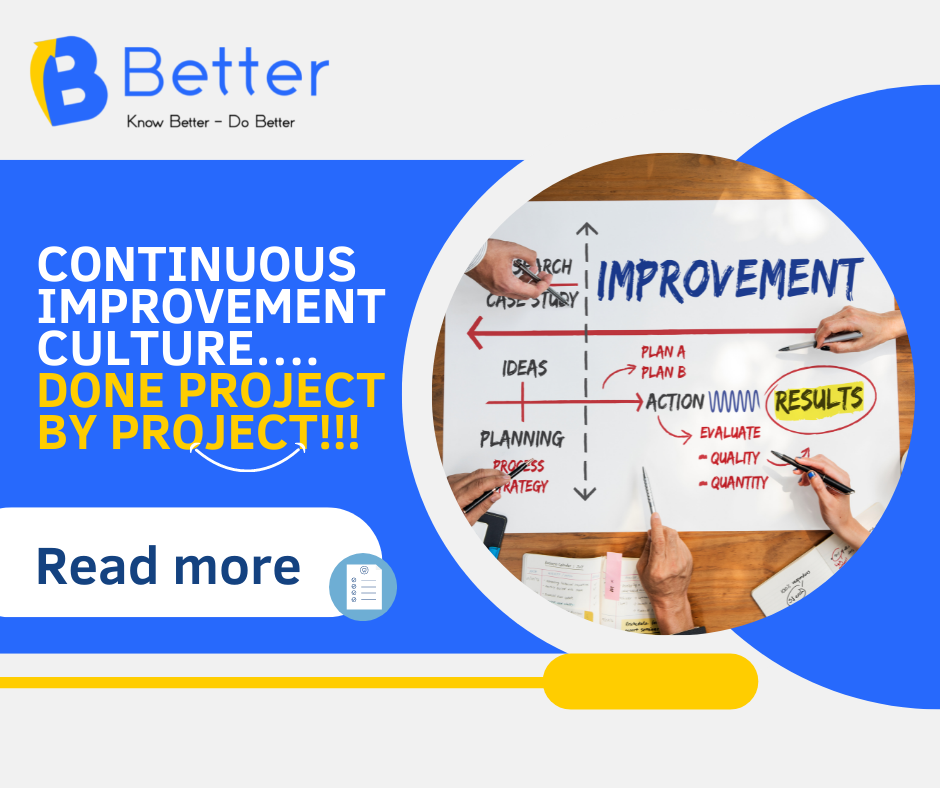
By MBB Carlos Ray Ruiz
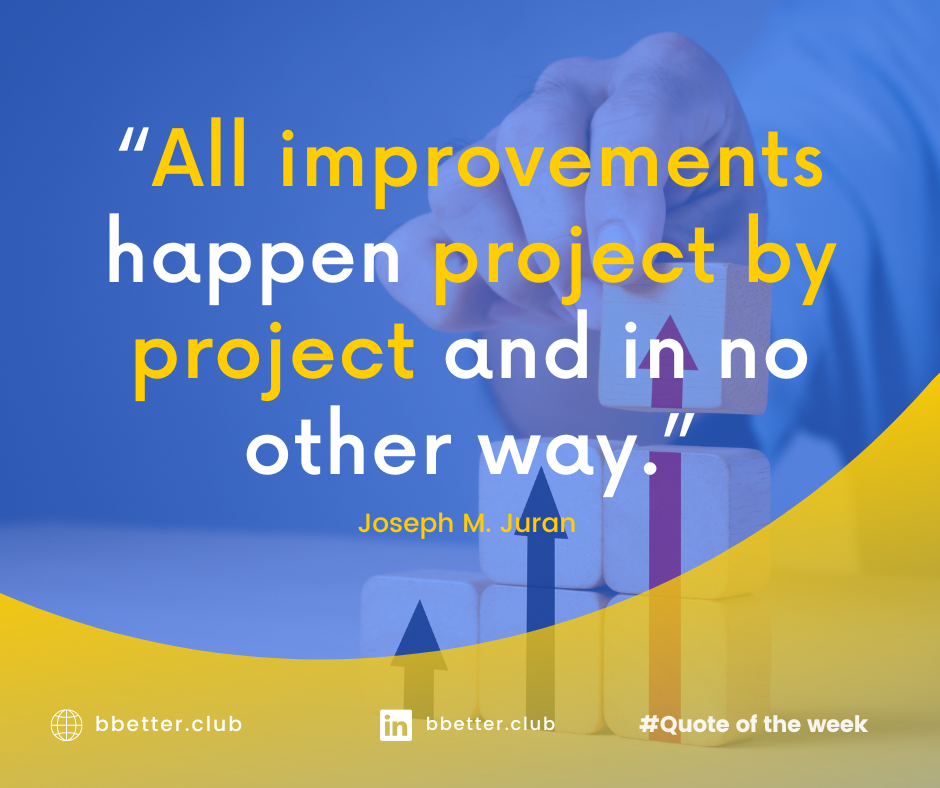
Many years ago after graduating from the university, I started working for Mabe, an organization that had a joint venture with General Electric. This happened when GE was introducing Six Sigma across the organization. On top of that, the organization I started working for was in the manufacturing field, where products, processes, time, and money were at the core of everything we did.
So as we began to deploy Six Sigma, the idea of each staff developing some kind of Continuous Improvement project became part of the culture of this organization. Often these projects were linked to a Lean Six Sigma certification process. So most of the decisions were driven within the context of those projects and it was likely that most of the employees will be leading or participating in one or more improvement projects on an ongoing basis.
Fast forward and after working for many organizations of different types, I see and recognize that this is not the way most organizations operate. On the contrary, it is very common for many organizations to rely on the expertise of managers and individuals to drive the operation and to drive whatever improvements they are willing and or capable to implement in the midst of many other priorities that compete with the need to improve their processes, products or services they offer to internal or external customers.
I have seen that this approach comes with lots of challenges, it becomes very challenging to attribute the success or failure of the leaders and managers to a particular system or process often blaming the leaders or the staff when goals are not met. It becomes hard to engage the staff with improvements since their leaders, managers, and staff view the idea of improving as something extra to their daily work. Improving becomes a burden and the organization is almost forced to invest and hire Project Managers, Business Analysis, Black Belts, etc. to lead their improvement efforts. Many times this approach prevents the organization to develop a strong Continuous Improvement culture since the responsibility to improve falls under these groups. Managers and leaders consider that the staff is too busy to develop and implement improvements to the products, processes, or services they offer.
So the following are 3 lessons I have learned on how to implement or strengthened a Continuous Improvement culture regardless of the type of industry you are in:
- Develop a strong yet simple Continuous Improvement – Project Management culture.
Improvements happen one project at a time and in no other way (Quote from Joseph M. Juran). Many organizations want to invest a lot of money in deploying and establishing a project management office (PMO). However, in my experience more important than having a group of project managers that have the tools and expertise to manage big projects, it is important to equip every staff member with a set of tools and principles to develop their own projects and view their job as a series of projects to improve and to achieve their team and individual goals. For example, the DMAIC methodology is a step-by-step methodology that could help transform the way people operate and do their job. Define, Measure, Analyze, Improve, and Control (DMAIC 2min video). This methodology is basically implementing a scientific method in the context of a business.
There are many models out there for all kinds of project management initiatives, it is important for organizations to stick with one methodology and to make that the standard across the enterprise. This will help the organization to speak the same language in regard to project management and Continuous Improvement.
2. Make your Continuous Improvement initiative, part of a career development program.
Organizations need to find ways to motivate, encourage and maintain the engagement of their staff. It is very common for many organizations to demand results falling short of how they invest and recognize their staff. Establishing a Project Management in combination with a Continuous Improvement culture will open great opportunities to reward and recognize your staff. One of the things that I have done with many of the organizations I have had the opportunity to participate in is to develop a Lean Six Sigma certification program that links Continuous Improvement efforts to their career development. I am not necessarily advocating for any particular program but I think that any organization will benefit by finding ways to use their Continuous Improvement – Project Management initiative and deployment to a specific reward and recognition program.
3. All leaders and managers are on top of their Continuous Improvement initiatives (Manage by improvements).
Many organizations make progress by first looking at ways to better measure important indicators that allow them to make better decisions and to better allocate resources.
Metrics and indicators are a great way to know if an organization is delivering the expected results. Many invest a huge amount of money and resources in establishing robust reporting systems. However, most organizations get stuck in this idea. They define metrics to measure results and they usually develop their entire management and leadership process around those metrics (lag metrics). Even though this is a good indication know if an organization is making progress toward a mature Continuous Improvement culture. I have seen great teams and great organizations move their emphasis and focus, instead of just looking at Key Performance Indicators, great organizations develop a strong Continuous Improvement management system where managers and leaders develop lead indicators that are deliberately linked to their Continuous Improvement initiative.
There are three questions that leaders need to be able to answer at any given time:
- What improvement projects are helping them to achieve their highly important goals?
- What is the status of those projects in regard to the DMAIC methodology (or the C.I. methodology chosen for this purpose)?
- What are the next projects that their teams are going to implement and what other improvement opportunities are lining up from the list of improvement opportunities?
To keep it simple, any leader at any time should be ready to provide a status of where they are in regards to their Continuous Improvement projects.
Conclusions
When organizations haven’t developed a Continuous Improvement process that could explain how all the leaders (top-down) will deliver consistent results, explained in clear and simple steps, then organizations are risking one of the most important keys to success. Great organizations concentrate on developing and perfecting their Continuous Improvement process so that day after they, month after month, and year after year, the organization becomes more consistent in its effectiveness to achieve great results to satisfy and enlighten their customer.