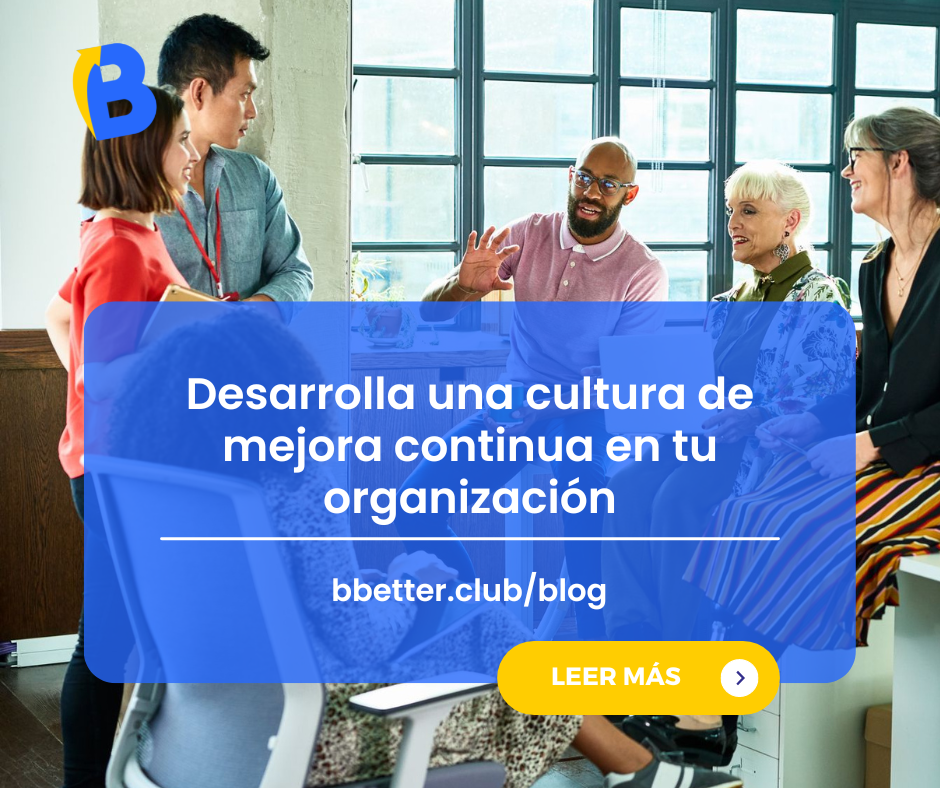
Equipos autodirigidos
Sensei – Marco Antonio Peña Alvarez

Prefacio
En los últimos 20 años el mundo ha cambiado drásticamente. El acceso a la información en las redes sociales define patrones de conducta y modelos de pensamiento de una forma que no imaginábamos en los 90’s. Como resultado de esta influencia ejercida por los “nuevos medios de comunicación” las culturas organizacionales hoy exigen un cambio radical, las herramientas de mejora continua que antes se utilizaban sólo en niveles de mandos medios y superiores tienen que ser conocidas y aplicadas por todos los miembros de una organización a través de una alineación de comportamientos que sostengan los indicadores de negocio, sin perder de vista las necesidades de realización y reconocimiento del personal.
La cultura organizacional y el conocimiento de los modelos de excelencia operacional deben ayudar para que las empresas e instituciones mantengan un alto nivel de competitividad en los mercados mundiales (los cuales son cada vez más flexibles e impredecibles al mismo tiempo), todas las organizaciones tienen que estar preparadas para hacer frente a nuevos modelos de pensamiento y comportamiento. Por lo anterior resulta esencial, así como llevar una nómina, asegurar que todo el staff participe activamente en estos nuevos modelos de cultura organizacional y mejora continua.
Cultura organizacional y el modelo de excelencia operacional
Introducción
Mi nombre es Marco Peña, en mis 17 años de experiencia en la industria manufacturera he ocupado varios cargos. He navegado por muchas áreas y funciones entre las que se encuentran, puestos técnicos como ingeniero en un laboratorio de confiabilidad donde trabajaba de cerca con la evaluación funcional de nuevos productos, realización de pruebas de confiabilidad para predecir los modos de falla funcionales y definir los tiempos de garantía de un producto, diseño de componentes y calidad de proceso, desarrollo de calidad de proveedores, desarrollo de manuales corporativos basados en las mejores prácticas y herramientas aplicadas por diferentes plantas manufactureras para garantizar los estándares y requerimientos de los clientes. En los últimos 10 años de mi carrera he estado liderando diferentes modelos de excelencia operacional, desde sistemas internos de mejora continua basados en herramientas de manufactura esbelta (Lean Manufacturing), hasta modelos que toman como referencia métodos y mejores prácticas del Sistema de Producción Toyota, hoy en día conocidos y difundidos ampliamente a través de conceptos como “SHINGO PRIZE” que es un sistema de trabajo y alineación institucional basado en los valores de la familia Toyoda.
A través de mi experiencia y a lo largo de los años, he podido observar como proyectos con una trascendencia global son implementados y sostenidos por todos los niveles de la organización, el modelo de excelencia operacional hoy en día exige un enfoque basado en una participación activa y comprometida por parte del personal operativo. En relación a este punto también he podido comprender que los valores de la organización, muchas veces “minimizados”, son esenciales para poder lograr la alineación y rumbo requeridos en cualquier negocio. Son los valores de la organización los que ayudan a definir el modelo de pensamiento y comportamiento mismos que van (o no) a asegurar el éxito y la sostenibilidad de cualquier organización.

Modelo de mejora continua: involucramiento y alineación – equipos auto dirigidos
Las herramientas y principios de la mejora continua tienen que ser apoyadas por los altos mandos de un negocio, es responsabilidad de los líderes de la organización, involucrar activa y proactivamente a todos los mandos medios y personal operativo. Parte esencial del crecimiento y adaptación de las nuevas instituciones, radica en el hecho de que toda persona tiene una capacidad ilimitada para resolver problemas. Todos como individuos lidiamos y nos enfrentamos a retos y problemas en nuestra vida diaria, incluso esos retos y problemas pueden llegar a ser mucho más complejos que a los problemas que nos enfrentamos en el ámbito laboral. Por lo anterior sabemos que cualquier persona tiene esa capacidad y en cierta manera tiene la responsabilidad de contribuir dentro de la organización a analizar problemas, generar ideas de mejora e implementar esas mejoras. A estas mejoras graduales y constantes se le conoce como Kaizen (Kai – Cambio, Zen – Bueno, Kaizen = Cambio Bueno o Mejora Continua).
Las ideas de mejora continua, administradas mediante sistemas sencillos pero bien fundamentados, ayudan para que el personal que conforma una organización, estén completamente alineados y enfocados en la mejora continua. El personal debe trabajar con objetivos claros, diarios, semanales, mensuales y anuales. Para que estos sistemas de mejora continua sean efectivos se debe contar con una comunicación efectiva entre áreas internas, lo que se conoce como relación cliente – proveedor, o enfoque al cliente interno, debido a esta necesidad (no negociable), las instituciones e industria manufacturera pueden funcionar de forma productiva e independiente trabajando bajo un esquema conocido como círculos de calidad, o como yo lo llamo, equipos auto dirigidos. Estos son equipos que trabajan en áreas funcionales con operaciones comunes. Dichos equipos de trabajo tienen métricas bien definidas, con objetivos tangibles y estratégicamente alineados a la visión e indicadores del negocio. Estos equipos trabajan bajo un esquema de ejecución de Gemba diario (Gemba – El piso de producción), revisión de indicadores en pizarrones estándar, y un enfoque en mejorar los indicadores que están directamente ligados a la Seguridad, Calidad, Producción, Costo y Gente (SCPCG).
Los equipos auto dirigidos deben tener una alineación estratégica tal que, en situaciones críticas operacionales, puedan tomar decisiones fundamentadas en el análisis de causa raíz, pero también, proactivamente desde la perspectiva de análisis de riesgo. Herramientas como AMEF (análisis de modo y efecto de la falla) y POKA-YOKE (a prueba de error), ayudan para que los equipos de trabajo puedan leer y entender los riesgos potenciales de sus operaciones, incluso antes de que impacten negativamente a la operación, ejecutando acciones que permitan minimizar los riesgos aun cuando el personal no tenga toda la experiencia trabajando directamente en la operación (personal nuevo).
El análisis de riesgo es fundamentado por estándares, procedimientos y entrenamiento del personal, no solo en instrucciones de trabajo (hojas de método) pero también en la aplicación de herramientas sencillas como 5S (orden y limpieza), Kaizen (mejora continua), 5 porqués, Ishikawa (causa y efecto) y A3 (análisis de causa raíz).
Todos los niveles de la organización participan en el monitoreo y control de los métricos mencionados anteriormente. Parte esencial en el funcionamiento de estos equipos autodirigidos, es el apoyo de los mandos medios o niveles administrativos, ya que en ellos recae la responsabilidad de ejecutar las acciones que apoyan las operaciones del día a día (conocidas en el mundo industrial como trabajo estándar). Para que los equipos auto dirigidos sean exitosos deben contar no solo con el compromiso y buena comunicación entre ellos, si no también, el apoyo de un “sponsor” (patrocinador) que los guíe y dirija efectivamente en el logro de los resultados (léase Seguridad, Calidad, Producción, Costo, Gente).
La efectividad debe ser medida de manera diaria, garantizando que las acciones de cada equipo están totalmente alineadas en conseguir y mantener los resultados en sus áreas de responsabilidad.
¿Cómo implementar un sistema de equipos auto dirigidos?
El sistema es técnicamente sencillo de implementar, la complejidad radica en el sostenimiento e involucramiento de todos los niveles de la operación, así es, lo he mencionado en repetidas ocasiones en este texto, el involucramiento de todo el personal, es esencial para que dicho sistema sea exitoso, operadores, mandos medios, gerencia y cada patrocinador de su respectivo equipo auto dirigido debe tener bien clara la importancia de participación para el éxito del equipo. La pregunta es, ¿cómo lograr ese involucramiento?, la respuesta es a través de un seguimiento diario mediante el Gemba (el piso de producción o donde las acción de los procesos pasan), el contacto directo con cada miembro del equipo, motivándolos a participar en las presentaciones de cierre y arranque de turno, invitándolos a cuestionar el estado actual, “forzando” la creatividad como principal elemento para la resolución de problemas. También es importante promover el apego a los estándares de trabajo y a las reglas del juego. Es muy importante asegurar que las expectativas sean claras y que se ejecuten por todos los integrantes de los equipos.
Es necesario entonces, definir qué indicadores de Seguridad, Calidad, Producción, Costo y Gente se estarán monitoreando por área, los miembros del staff y patrocinadores de cada equipo de trabajo deben garantizar que el personal a su cargo participa activamente. Además, debe quedar claro que estas responsabilidades no son negociables sino que son parte de su descripción de puesto. Incluso desde la contratación estas reglas deben quedar definidas como parte fundamental del modelo administrativo de la organización. Los métricos y evaluaciones anuales de cada empleado deben considerar la participación activa en el sistema de equipos auto dirigidos, dichos métricos deben reflejarse en un tablero de resultados conocido como “scorecard”, el cual tiene que ser visible en todos los niveles de la organización. El conocimiento de la tendencias de estos indicadores establecidos genera de manera natural un interés, una motivación y un sentido de pertenencia para todo el personal involucrado.
Como herramienta de análisis y solución de problemas, es necesario generar entrenamientos internos o dependiendo el caso, con consultores expertos en el tema. Dada mi experiencia, yo recomiendo antes de utilizar herramientas complejas, entrenar al personal operativo y mandos medios en el uso de las herramientas más sencillas tales como, 5S, Kaizen, Trabajo Estándar, Ishikawa, 5 Porqués, 8 Desperdicios, etc.
Pasos para la implementación
A partir de los puntos que he comentado con anterioridad, presento algunos pasos que son importantes considerar para la implementación de los equipos autodirigidos:
- Delimitar las funciones naturales de cada proceso interno en su operación (relación cliente proveedor)
- Definir miembros activos de equipos de trabajo que por sus funciones lograran alinearse estratégicamente a los objetivos del negocio (monitoreados a través de pizarrones sencillos y estandarizados con secciones para cada área antes mencionada SCPCG)
- Establecer los equipos de soporte y sus patrocinadores
- Estructurar y generar sistemas internos de desarrollo de personal (incluyendo funciones operativas y herramientas de análisis y solución de problemas).
- Revisión mensual de resultados, donde cada equipo auto dirigido está obligado a presentar la tendencia de los indicadores de su área, incluyendo un proyecto “Kaizen” en el que se ha demostrado la aplicación de las herramientas sistémicas en las que fueron entrenados, y validando un beneficio para alguno de los indicadores ya mencionados.
Hablando particularmente del paso número 5 en relación a la presentación mensual, es necesario, que todos los equipos auto dirigidos participen activamente en este espacio de tiempo, ya que en dicha revisión los evaluadores serán los miembros del equipo gerencial. El director de la organización también debe de participar activamente en estas presentaciones. De esta forma cada equipo auto dirigido tendrá la oportunidad de expresar también sus inquietudes basadas en el desempeño de cada área y también podrá expresar su sentimiento en relación al involucramiento de su respectivo equipo de soporte y a los apoyos que brindan al equipo en el día a día.
En la revisión mensual, me ha funcionado tener una clara definición y apego a un formato de presentación y evaluación estándar. Por lo tanto, es necesario que se establezca una agenda bien definida, la cual deberá incluir tiempos de presentación así como la secuencia de los equipos que van a presentar. Previo a la presentación cada equipo deberá alimentar de manera continua los indicadores con su respectiva tendencia así como la evidencia para demostrar dichas tendencias, algunos de los elementos que recomiendo incluir en estas presentaciones son:
- Cumplimiento de auditorías de proceso
- Auditorías de 5S
- Auditorías de seguridad
- Detección de riesgos
- Calibración de equipos de cada área
- Cumplimiento del mantenimiento autónomo
Cada uno de los elementos definidos tendrá un % de ponderación individual el cual será evaluado por cada integrante de las diferentes gerencias mediante un formato estándar de evaluación también definido con anterioridad.
Una regla de oro al hacer la revisión mensual es que esta reunión tenga como propósito invitar y motivar a que las personas liberen su potencial de creatividad y que sistemáticamente, se lleve a cabo la ejecución del análisis y solución de problemas. Esta no es una junta de quejas, todo lo contrario, es el tiempo requerido para tener ese acercamiento entre todos los niveles de la organización y donde todos a través de una competencia sana presentan los indicadores alineados a los objetivos del negocio. En esta presentación mensual se recibe retroalimentación directa en ambos sentidos (del personal que está directamente manejando los procesos hacia los gerentes y directivos y viceversa). Con el tiempo he aprendido que la metodología de equipos autodirigidos es una herramienta sistemática de comunicación efectiva, enfocada en analizar los problemas y evaluar las soluciones de manera conjunta, sin buscar culpables sino enfocando todos los esfuerzos del personal, en el análisis de causa raíz y en la ejecución de acciones de mejora.
Al final de esta presentación mensual y como resultado de esta competencia entre equipos autodirigidos, se seleccionan los mejores 3 lugares y una vez evaluados se presentan los resultados otorgando premios que motivan al personal a seguir trabajando y mejorando de forma diaria. Esta fase de reconocimiento invita al personal a seguir esforzándose por concretar resultados en su área y seguir viendo el Kaizen como una herramienta para lograr las mejoras de su área y como el veiculo para alcanzar la excelencia operativa de la organización.
Conclusión
Hemos aprendido que los modelos de mejora continua y excelencia operacional se apoyan y se fortalecen a través de la creación de equipos autodirigidos. Y que para poder implementar estos equipos se requiere de forma resumida:
- Definición clara de indicadores de negocio, y la alineación de estos indicadores.
- Definición de funciones, roles y responsabilidades, y una capacitación efectiva.
- Involucramiento de todos los niveles de la organización.
- Estándares bien definidos para el seguimiento y evaluación de resultados.
- Comunicación efectiva y reconocimiento del personal
Estos elementos hacen que las organizaciones no solo estén enfocadas en las necesidades de los clientes externos y usuarios finales de productos y servicios, también promueve el enfoque del proceso cliente proveedor interno, potencializando y maximizando la participación de todos y cada una de las personas que laboran en la organización. De esta forma, y con el debido sostenimiento de estos equipos autodirigidos, podremos decir que estamos francamente caminando en la dirección de la mejora continua. Es a través de este proceso sistemático y este cambio cultural que se podrán sostener los indicadores del negocio. Este sostenimiento se dará de forma diaria, mensual, anual y de forma continua. Por todo lo anterior podemos afirmar que la excelencia operacional es un modelo fundamental de un negocio, que tiene como objetivo competir, brindar resultados y beneficios medibles para satisfacer así a sus clientes y socios, ayudando así a que las organizaciones logren mantener su competitividad y liderazgo en los mercados donde se desarrollan.
Contacta a Marco directamente: marcopenaalvarez@hotmail.com
Visitalo en su Linkedin: Cuenta Linkedin Marco Peña