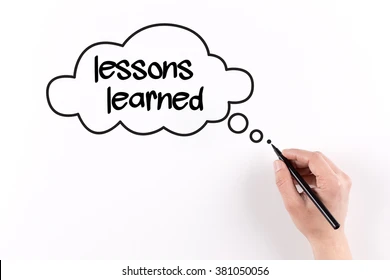
Project Management; Lessons Learned by Albert Guaravage
After nearly a decade as a finance controller with an agricultural manufacturing conglomerate, I came to the realization much of my time was spent on “projects” that could be categorized as “process improvement”. While I have my MBA, I realized I did not have a clear/structured understanding of how to effectively implement both projects or process improvements. After talking to one of my mentors he recommended I become certified as a PMP (Project Management Professional), and Lean Six Sigma Green Belt.
After pitching the benefits of these certifications to management I received the green light to pursue both certifications, starting with my PMP. I enrolled in a week-long, in-person boot camp class with the Project Management Institute to kickstart my training. Like all such classes, they are much like trying to drink from a firehose, so once completed I took two months to study the PMBOK (Project Management Body of Knowledge). I found the review videos and quizzes offered on the Educate 360 Learner Dashboard especially helpful in getting my knowledge up to a point where I felt comfortable taking and passing the exam.
Since becoming certified I have become more precise in recording the scope of projects, working together with stakeholders to ensure I fully understand all requirements and obtaining a clear DOD (Definition of Done). Just having these small processes in place has given me more confidence in taking on process improvement projects. Next step: Lean Six Sigma Green Belt certification!
Lessons Learned:
- Many tasks, even small ones we do as part of our regular day-to-day workload, can be done more efficiently if we apply the principles of project management.
- Don’t assume management is unable to see the value of continued education. Ensure you pitch them with relevant examples of how it will improve your productivity or quality of work.
- The PMP places a large emphasis on Agile methodology. Just because Agile is often associated with the software development field, don’t write it off. There are many parts of Agile that can be used in different industries. Take the lessons learned and tailor them to your particular job.